MTU Aero Engines fertigt Turbinenzwischengehäuse für Langstrecken-Antriebe
München, 26. Juni 2015 – Die MTU punktet im oberen Schubbereich: Deutschlands führender Triebwerkshersteller entwickelt und fertigt Turbinenzwischengehäuse (TCF = Turbine Center Frame) für Langstrecken-Triebwerke. In München entstehen die TCF des GP7000 (Airbus A380), des GEnx (Boeing 787 Dreamliner und Boeing 747-8) und des GE9X, Exklusivantrieb der Boeing 777X.
„Das Turbinenzwischengehäuse bildet den Kanal für das von der Hochdruckturbine in die Niederdruckturbine strömende Heißgas. Die MTU verfügt über eine langjährige Erfahrung für diese äußerst anspruchsvolle Triebwerkskomponente, bei der sehr enge Bauteiltoleranzen gefordert werden“, erklärt MTU-Technikvorstand Dr. Rainer Martens. Das Strukturbauteil setzt sich im Wesentlichen aus zwei Teilegruppen zusammen: Hub Strut Case (HSC) und Flowpath Hardware (FPH). Das HSC ist das tragende Element und besteht aus einem Gehäuse mit mehreren Stützstreben sowie einer Nabe, in die das Lager eingebaut ist. Die FPH setzt sich aus Gußteilen zusammen, die den gasführenden Kanal bilden.
Der Gesamtverbund des Turbinenzwischengehäuses hat vielfältige Aufgaben zu bewältigen: TCF müssen die heißen Gase, die die Hochdruckturbine mit einer Temperatur von mehr als 1.000 Grad Celsius verlassen, mit möglichst geringen aerodynamischen Verlusten an Strukturbauteilen und Leitungen vorbei zur Niederdruckturbine leiten. Beide Turbinen gilt es mit Kühlluft zu versorgen, deren Zufuhr durch das TCF erfolgt. Als tragende Struktur nimmt das TCF das hintere Lager der Hochdruckwelle auf und trägt damit maßgeblich zur Spalthaltung in den Hochdruckkomponenten bei. Das stellt große Herausforderungen an die Fertigungsgenauigkeit und Umfangssymmetrie des Designs. Da das TCF das Lager der Hochdruckwelle trägt, muss die Ölzu- und -abfuhr durch die heiße Struktur sichergestellt werden. Zudem gilt es, große Lasten abzufangen, die zum Beispiel im Falle eines Fan Blade Out, dem Verlust einer Fan-Schaufel, entstehen. Martens: „Turbinenzwischengehäuse sind im Betrieb extremen Belastungen ausgesetzt - hoher mechanische Beanspruchung und hohen Temperaturen. Werkstoff und Konstruktion müssen höchsten Ansprüchen genügen, was wiederum eine Fertigung auf höchstem Niveau erfordert. Die haben wir in München aufgebaut.“
Startschuss: GP7000
Eingestiegen ist die MTU in die Entwicklung und Fertigung von Turbinenzwischengehäusen mit der Beteiligung am GP7000 für die A380, das größte Passagierflugzeug der Welt. Als Programmpartner sowohl von GE Aviation als auch Pratt & Whitney übernahm der deutsche Triebwerksexperte die Verantwortung für die komplette Niederdruckturbine, die Fertigungsverantwortung für Teile der Hochdruckturbine sowie die Gesamtverantwortung für das TCF. Das Turbinenzwischengehäuse des GP7000 basiert auf dem GE90-TCF und wurde von der MTU überarbeitet. „Durch einfachere Bauweisen sowie geschickte Teileoptimierung konnten wir Gewicht und Kosten reduzieren“, informiert Wolfgang Hiereth, Leiter GE-Programme bei der MTU. Bis zum Frühjahr 2015 hat die MTU circa 400 GP7000-TCF gefertigt; etwa 350 weitere sollen folgen. Der Mega-Airbus befindet sich seit 2008 im Linieneinsatz.
Fertigung in Rekordzeit: TCF für das GEnx
Im Jahr 2008 übertrug GE Aviation der MTU die Verantwortung für das TCF eines weiteren Triebwerksprogramms - des GEnx für den Boeing 787 Dreamliner und die Boeing 747-8. „Dieses TCF ist ebenfalls eine GE-Entwicklung, die wir technisch überarbeitet haben“, informiert Dr. Claus Riegler, Leiter Entwicklung Zivile Programme bei der MTU. Ergebnis: Das MTU-TCF sieht von außen aus wie das von GE - aber mit modifiziertem Innenleben. Riegler: „Zum einen haben wir die Flow-Path-Hardware optimiert, deren Herstellung aufgrund der komplexen Form extrem anspruchsvoll ist. Das verbessert den Wirkungsgrad. Zum anderen konnten wir auch hier das Gewicht des gesamten Moduls durch konstruktive Änderungen verringern.“
Gefertigt wird das GEnx-TCF auf zwei hochmodernen Fertigungslinien in München. Die Programmmeilensteine wurden in schnellem Tempo erreicht: Ende August 2011 ging das erste Serienmodul an GE und bereits neun Monate später – im Mai 2012 – wurde der erste Cargolux-Frachter, eine Boeing 747-8F, mit einem MTU-TCF ausgeliefert. Im August 2012 erhielt GE Aviation das 100. MTU-Modul. „Das alles haben wir in Rekordzeit geschafft“, kommentiert Hiereth. In den Münchner Hallen wird täglich ein GEnx-TCF fertiggestellt; insgesamt wurden hier bis April 2015 über 700 Exemplare montiert. Der GEnx-Gesamtmarkt wird auf etwa 4.400 Triebwerke geschätzt. Und die Erfolgsgeschichte geht weiter: Im November 2014 unterzeichnete die MTU mit GE Aviation einen Vertrag über die Instandhaltung ihres Bauanteils. Damit ist Deutschlands führender Triebwerkshersteller MRO-Dienstleister im weltweiten Netzwerk auch für dieses Turbinenzwischengehäuse.
Meisterstück für GE9X
Das technologisch anspruchsvollste Turbinenzwischengehäuse entwickelt und fertigt die MTU für das GE9X. Dieses Triebwerk wird exklusiv die Boeing 777X in die Luft bringen und im Verhältnis von Kraftstoffverbrauch zu Schubkraft das effizienteste Triebwerk sein, das GE jemals auf den Markt gebracht hat. Im Juli 2014 hat die MTU die Entwicklungs- und Fertigungsverantwortung für dieses Triebwerksmodul übernommen. Basierend auf der Grundarchitektur des GEnx-TCF wird es umfangreiche Optimierungen geben, um Wirkungsgrad und Produktion weiter zu verbessern. Riegler: „Ausgehend vom GEnx-TCF sprechen wir von einem Evolutionsschritt.“ Bauweisen sollen optimiert und ein anderes Aufhängungskonzept erarbeitet werden; Teile könnten additiv hergestellt werden. Martens: „Mit der GE9X-Programmbeteiligung haben wir uns einen entscheidenden Marktanteil an einem der wichtigsten künftigen Antriebe im oberen Schubbereich gesichert und erreichen damit einen noch ausgewogeneren Mix unseres Produktportfolios.“ Zum Zeitplan: Das GE9X soll 2020 auf den Markt kommen; 400 Flugzeuge sind bereits fest bestellt und optioniert. Die Auslieferung der ersten MTU-Entwicklungsmodule ist für nächstes Jahr geplant.
Über die MTU Aero Engines
Die MTU Aero Engines AG ist Deutschlands führender Triebwerkshersteller. Die Kernkompetenzen der MTU liegen bei Niederdruckturbinen, Hochdruckverdichtern, Turbinenzwischengehäusen sowie Herstell- und Reparaturverfahren. Im zivilen Neugeschäft spielt das Unternehmen eine Schlüsselrolle bei der Entwicklung, Fertigung und dem Vertrieb von Hightech-Komponenten im Rahmen internationaler Partnerschaften. MTU-Bauteile kommen bei einem Drittel der weltweiten Verkehrsflugzeuge zum Einsatz. Im Bereich der zivilen Instandhaltung zählt das Unternehmen zu den Top 5 der weltweiten Dienstleister für Luftfahrtantriebe und Industriegasturbinen. Die Aktivitäten sind unter dem Dach der MTU Maintenance zusammengefasst. Auf dem militärischen Gebiet ist die MTU Aero Engines der Systempartner für fast alle Luftfahrtantriebe der Bundeswehr. Die MTU unterhält Standorte weltweit; Unternehmenssitz ist München. Im Geschäftsjahr 2014 haben rund 9.000 Mitarbeiter einen Umsatz in Höhe von rund 3,9 Milliarden Euro erwirtschaftet.
Media
Kontakt
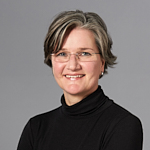
Pressesprecherin Technologie