MTU Aero Engines entwickelt und betreibt einzigartiges Triebwerksmontagesystem
- Höchste Ansprüche an Flexibilität, Ergonomie, Skalierbarkeit und Digitalisierung
- Ein Drittel aller A320neo-Getriebefans werden in München zusammengebaut
München, 5. November 2019 – Mit dem Getriebefan (GTF) realisieren Pratt & Whitney und die MTU Aero Engines die öko-effizientesten Triebwerke, die es derzeit auf dem Markt gibt. Die MTU steuert zu dieser Antriebsfamilie nicht nur Turbinen- und Verdichter-Schlüsseltechnologien bei, sondern zeichnet auch für die Endmontage eines Drittels aller PW1100G-JM-Getriebefans für den Airbus A320neo verantwortlich. „Dafür haben wir ein hochmodernes bodengeführtes Linien-Montagesystem selbst entwickelt, am Unternehmenssitz in München aufgebaut und in Betrieb genommen“, erklärt Lars Wagner, Technik-Vorstand der MTU. „Es entspricht den neuesten technologischen sowie ergonomischen Standards und ist weltweit einzigartig.“
Kernstück der GTF-Serienmontage der MTU ist ein hochinnovatives, ferngesteuertes, bodengeführtes Linienmontagesystem, das mit dem Bauzustand des Triebwerkes modular wächst. „Dieses System wurde auf wenig Fläche in ein bestehendes Gebäude eingepasst“, informiert MTU-Produktionsleiter Ulrich Peters. Der Zusammenbau eines Triebwerks erfolgt in mehreren Arbeitsschritten. Zudem können mehrere PW1100G-JM-Triebwerke gleichzeitig in unterschiedlichen Bauzuständen montiert werden. Peters: „In der Endausbaustufe werden hier 80 Mitarbeiter beschäftigt sein. Pro Tag soll ein komplettes Triebwerk die Linie verlassen.“ Die neue Montagelinie ist die erste zivile Endmontage in der 85-jährigen MTU-Geschichte und seit Ende 2016 in Betrieb. Seitdem haben rund 300 Triebwerke die Halle verlassen. Im Schnitt werden 20 Triebwerke pro Monat zusammengebaut.
Innovatives bodengeführtes Liniensystem
Die Eigenentwicklung war erforderlich geworden, da es auf dem Markt kein für die MTU passendes Endmontagesystem gab: Die meisten Linien arbeiten mit deckengeführten Systemen – so auch die beiden anderen GTF-Montagelinien von Pratt & Whitney in den USA. „Für die MTU kamen solche Systeme nicht in Frage, denn sie verfügen nicht über die Flexibilität, die wir benötigen“, erklärt Elmar Stichlmair, Projektleiter Industrialisierung A320neo-GTF und geistiger Vater der Anlage. Wichtig war der MTU auch das flexible Ein- und Ausschleusen von Triebwerken.
Das MTU-Montagesystem verzichtet auf aufwändige Decken-Kran-Konstruktionen, sondern setzt auf ein bodengeführtes System. Der Zusammenbau der Triebwerke erfolgt automatisiert, papierlos und nach den modernsten ergonomischen Erkenntnissen unter Einbeziehung innovativer Montagetechnologien sowie digitaler Werkzeuge. Stichlmair: „Arbeitspläne, Laufkarten, Montageschritte – alles ist miteinander verknüpft und digital abgebildet.“ Bildschirme informieren die Mitarbeiter über die einzelnen Schritte und den Status quo.
Mobilität mit speziell entwickelten Wagen
Den sicheren Transport am Boden gewährleisten neuartige Transportwagen, die die MTU-Experten ebenfalls selbst entwickelt haben. Das sogenannte Floor Based Transportation System (FBTS) besteht aus 16 einzelnen Carriern, die je nach Arbeitsfortschritt passend gekoppelt werden und sich entlang der Montagelinie bewegen. Stichlmair: „Jeder Carrier kann sich in jede Richtung bewegen und ist für sich ferngesteuert. Er kann einzeln aber auch in unterschiedlichen Verbünden angesteuert und betrieben werden.“ Einzelne Triebwerke können zu jeder Zeit aus- und eingeschleust werden.
Eine der größten Herausforderungen bestand darin, die Triebwerke sicher aufzunehmen und zu gewährleisten, dass sie durch Fahrbewegungen nicht beschädigt oder verspannt werden. Gelöst wurde dieses Problem durch eine speziell dafür entwickelte Triebwerkslagerung, die den Antrieb zu jeder Zeit 100 Prozent spannungsfrei hält. Die Steuerung ist kompakt und erfüllt alle sicherheitstechnischen Anforderungen. Die Steuermodule interagieren zwischen den Einheiten.
Smarte Fertigung
Beispiele smarter Elemente hinsichtlich Digitalisierung und Automatisierung sind punktgenaues und komplett systemgesteuertes induktives Heizen der Bauteile vor dem Fügen, effiziente und systemunterstütze Vollständigkeitsprüfung per Tablet sowie die digital gesteuerte Verschraubung per Barcode-Scan, die die Mitarbeiter von Schritt zu Schritt leiten und abweichende Einstellungen per Hand verhindern. Der Vorteil: Anziehprozesse von Schraubverbindungen laufen hochpräzise, drehmomentgesteuert und automatisiert ab.
Das bodengeführte Serienendmontagesystem der MTU hat Potenzial: Es wird konsequent weiterentwickelt und stets auf den technologisch neuesten Stand gebracht; bei Bedarf kann es problemlos auch für andere Triebwerksmuster skaliert werden. Geeignet ist es auch für die Triebwerksinstandsetzung.
Kontakt
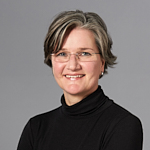
Pressesprecherin Technologie
Über die MTU Aero Engines
Die MTU Aero Engines AG ist Deutschlands führender Triebwerkshersteller. Die Kernkompetenzen der MTU liegen bei Niederdruckturbinen, Hochdruckverdichtern, Turbinenzwischengehäusen sowie Herstell- und Reparaturverfahren. Im zivilen Neugeschäft spielt das Unternehmen eine Schlüsselrolle mit der Entwicklung, Fertigung und dem Vertrieb von Hightech-Komponenten im Rahmen internationaler Partnerschaften. MTU-Bauteile kommen bei einem Drittel der weltweiten Verkehrsflugzeuge zum Einsatz. Im Bereich der zivilen Instandhaltung zählt das Unternehmen zu den Top 5 der weltweiten Dienstleister für Luftfahrtantriebe und Industriegasturbinen. Die Aktivitäten sind unter dem Dach der MTU Maintenance zusammengefasst. Auf dem militärischen Gebiet ist die MTU Aero Engines der Systempartner für fast alle Luftfahrtantriebe der Bundeswehr. Die MTU unterhält Standorte weltweit; Unternehmenssitz ist München. Im Geschäftsjahr 2018 haben rund 10.000 Mitarbeiter einen Umsatz in Höhe von rund 4,6 Milliarden Euro erwirtschaftet.