Additive Fertigung: MTU Aero Engines stärkt Aktivitäten
München, 22. Mai 2018 – Das Boroskopauge für den A320neo-Getriebefan war der Durchbruch, jetzt intensiviert die MTU Aero Engines ihr Engagement im Bereich Additive Fertigung: Seit Anfang dieses Jahres beschäftigt sich eine eigene Abteilung mit diesem Thema. Die Leitung hat Dr. Jürgen Kraus übernommen. „Mit der Bündelung aller Aktivitäten von der Auslegung über die Technologieentwicklung bis hin zur Serienfertigung in einer organisatorischen Einheit wollen wir unseren Vorsprung halten und weiter ausbauen“, kommentiert MTU-Technik-Vorstand Lars Wagner.
Dr. Jürgen Kraus, Leiter Additive Fertigung, hat am Unternehmenssitz in München rund 30 Personen um sich geschart – Experten aus unterschiedlichen Fachdisziplinen: Konstrukteure, Strukturmechaniker, Verfahrensspezialisten und Arbeitsplaner. Sie konzipieren neue Anwendungen und Bauweisen nach bionischen Gesichtspunkten, treiben die Weiterentwicklung der Fertigungstechnologie voran und industrialisieren die komplette Prozesskette. Der Einsatz lohnt sich: Experten schätzen, dass bis 2030 mindestens 15 Prozent eines Triebwerks aus additiven Teilen bestehen. „Mit der Entwicklung neuer Maschinentypen sowie einer verbesserten Online-Prozesskontrolle können immer mehr Bauteile wirtschaftlich additiv gefertigt werden“, erklärt Dr. Jörg Henne, Leiter Entwicklung und Technologie. Bei der MTU kommt das Selektive Laserschmelzen (Selective Laser Melting = SLM) zum Einsatz; seit 2013 läuft die Serienfertigung von Boroskopaugen für den A320neo-Getriebefan PurePower®PW1100G-JM.
Deutschlands führender Triebwerkshersteller hat viel vor: „Wir entwickeln das additive Verfahren mit hoher Priorität in zahlreichen Technologieprojekten und Technologieförderprogrammen weiter“, erläutert Technik-Vorstand Wagner. Es geht um neue Designs, neue Bauteile und neue Werkstoffe. Im Rahmen des größten europäischen Technologieförderprogramms Clean Sky arbeitet die MTU etwa an einem additiv gefertigten Dichtungsträger: Der Innenring mit integralen Honigwaben soll im Hochdruckverdichter verbaut und zu einer verbesserten Spalthaltung und damit einer Wirkungsgraderhöhung beitragen. Weitere Bauteile, wie Lagergehäuse, Halterungen und Streben, sollen folgen. Zudem gilt es, die Prozessüberwachung weiter auszubauen und eine Verbesserung der Oberflächengüte herbeizuführen.
Bestechende Vorteile
Die MTU beschäftigt sich seit über zehn Jahren mit additiven Fertigungsverfahren, denn sie verfügen über bestechende Vorteile: Mit ihnen können komplexe Bauteile, die herkömmlich nicht oder nur sehr aufwendig zu fertigen sind, mit geringerem Material- und Werkzeugeinsatz hergestellt werden. Die Realisierung neuer Designs wird möglich, Entwicklungs-, Fertigungs- und Lieferzeiten verkürzen sich deutlich und die Herstellkosten sinken. Kraus: „Begonnen haben wir mit der Herstellung von Werkzeugen, etwa Spritzdüsen und Schleifscheiben, sowie einfachen Bauteilen für Entwicklungsversuche.“ In der zweiten Phase wurden Guss- und Frästeile substituiert. In diese Etappe fallen auch die Getriebefan-Boroskopaugen. Im nächsten Schritt sollen Leichtbauteile neuentwickelt und gefertigt werden. Wagner: „Die MTU wird ihr Bauteilspektrum sukzessive erweitern.“
Über die MTU Aero Engines
Die MTU Aero Engines AG ist Deutschlands führender Triebwerkshersteller. Die Kernkompetenzen der MTU liegen bei Niederdruckturbinen, Hochdruckverdichtern, Turbinenzwischengehäusen sowie Herstell- und Reparaturverfahren. Im zivilen Neugeschäft spielt das Unternehmen eine Schlüsselrolle mit der Entwicklung, Fertigung und dem Vertrieb von Hightech-Komponenten im Rahmen internationaler Partnerschaften. MTU-Bauteile kommen bei einem Drittel der weltweiten Verkehrsflugzeuge zum Einsatz. Im Bereich der zivilen Instandhaltung zählt das Unternehmen zu den Top 5 der weltweiten Dienstleister für Luftfahrtantriebe und Industriegasturbinen. Die Aktivitäten sind unter dem Dach der MTU Maintenance zusammengefasst. Auf dem militärischen Gebiet ist die MTU Aero Engines der Systempartner für fast alle Luftfahrtantriebe der Bundeswehr. Die MTU unterhält Standorte weltweit; Unternehmenssitz ist München. Im Geschäftsjahr 2017 haben rund 10.000 Mitarbeiter einen Umsatz in Höhe von rund fünf Milliarden Euro erwirtschaftet.
Kontakt
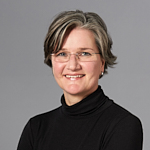
Pressesprecherin Technologie