Lightweight aircraft engines of the future: MTU, DLR, GKN further enhance the engine compression system in the frame of the EU-technology program Clean Sky 2
• ICD rig begins test operations at DLR in Cologne
• New technologies for next-generation geared turbofan engines
Munich, December 19, 2017 – Making good things even better - under the European Clean Sky 2 research program, long-term partners MTU Aero Engines, German Aerospace Center (Deutsches Zentrum für Luft- und Raumfahrt (DLR)), and GKN Aerospace Engine Systems, Sweden have joined forces to enhance an engine’s compression system and make it lighter. The new technologies could already go into the next generation of geared turbofan engines. At the DLR site in Cologne, the test campaign on the ICD rig has now officially kicked off.
ICD stands for Inter Compressor Duct and is the name of the transition channel between the low- and high-pressure compressors. The goal is to precisely fine-tune the interaction of the low-pressure compressor, ICD and high-pressure compressor to identify and leverage new potential for even more fuel-thrifty engines. An important step in this direction is the systematic mapping of the flow conditions in short, steep transition channels (ICDs). To this aim, an entirely new wind-tunnel test rig was built at DLR Institute of Propulsion Technology in Co-logne, MTU’s Center of Competence (CoC) for propulsion systems.
Representatives from the three partners – MTU, DLR, and GKN Aerospace Engine Systems –witnessed the official launch of the test operations. For MTU, being the lead party in the project, Dr. Gerhard Ebenhoch, Director Technology Management, stated: “This cooperation combines the partners’ respective strengths – GKN’s expertise in large static components, DLR’s experience in testing, and MTU’s expertise in compressors and systems – in an exemplary manner.”
For the DLR, Prof. Rolf Henke, Executive Board Member responsible for aeronautics research says: “As a national research center, DLR plays a key role in the progressive development of the entire air transport system. There have been great advances in propulsion in recent decades. Together with our partners MTU and GKN, we are very proud to introduce it a further large step with this ICD rig.” And for GKN Aerospace Engines Robert Lundberg adds: “To be able to validate our technologies at high TRL in a unique rig is really an opportunity for GKN. We have no chance to do this in Sweden, so it really shows the importance of European collaboration.”
For Clean Sky the Project Officer of the Engine-ITD Jean-Francois Brouckaert acknowledged: “This new test facility allows to perform important EU collaborative research on the next generation of engines. Congratulations to the MTU, DLR and GKN team for achieving this important milestone! It is an excellent example of complementarity between experimental and numerical work.”
Measurement technology at the highest level of detail
The ICD rig measures the channel flow in an unprecedented depth of detail: 500 pressure tapping points, probe measurements at three traversal levels, the use of laser technology and turbulence probes allow detailed insights in the flow mechanisms. Dr. Gerhard Kahl, Chief Engineer, Technology Demonstrators and Rigs at MTU is certain: “By conducting these tests, we’ll certainly gain a much better understanding of the flow conditions in the ICD, the aim being to come up with particularly compact designs to further reduce the length, and hence the weight, of the engines in the future.”
In a next step, three different ICD configurations will be tested over the course of next year. Based on the ICD rig test results obtained, a two-shaft test rig will be designed in 2019 and built one year later. From 2021 on, the low- and high-pressure compressors will be tested together as one entity.
Launched in 2014, the Clean Sky 2 technology program is part of the EU’s Horizon 2020 Framework Program for Research and Innovation and is slated to run through 2024. It is the successor to Clean Sky 1, the European Union’s largest-ever aeronautics research program. The overall objective is to make aviation even cleaner and more efficient. MTU is one of 16 lead partners and is responsible for the ICD test rig that has now begun test operations, plus an engine demonstrator. Core partners are the DLR (Deutsches Zentrum für Luft- und Raumfahrt) and GKN Aerospace Engine Systems.
About MTU Aero Engines
MTU Aero Engines AG is Germany’s leading engine manufacturer. The company is a technological leader in low-pressure turbines, high-pressure compressors, turbine center frames as well as manufacturing processes and repair techniques. In the commercial OEM business, the company plays a key role in the development, manufacturing and marketing of high-tech components together with international partners. Some 30 percent of today’s active aircraft in service worldwide have MTU components on board. In the commercial maintenance sector the company ranks among the top 5 service providers for commercial aircraft engines and industrial gas turbines. The activities are combined under the roof of MTU Maintenance. In the military arena, MTU Aero Engines is Germany’s industrial lead company for practically all engines operated by the country’s military. MTU operates a network of locations around the globe; Munich is home to its corporate headquarters. In fiscal 2016, the company had a workforce of some 9,000 employees and posted consolidated sales of approximately 4.7 billion euros.
Contact
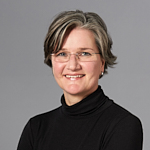
Press Officer Technology