Joint research project LeiLa: MTU develops technologies for quieter engines
• Partners working on innovative solutions for next-generation propulsion systems
Munich, October 21, 2016 – With the PurePower® PW1000G geared turbofan (GTF) engine, Pratt & Whitney and MTU Aero Engines are building the engine for the future. The new technology cuts fuel burn and CO2 emissions by 16 percent and reduces noise footprint levels by 75 percent. But this is not where the research effort ends: Just recently, the LeiLa (Leiser Luftfahrtantrieb: quiet aircraft propulsion) project was successfully completed. The big players in the industry joined forces with partners from research and academe to develop innovative solutions already set to be incorporated into the next generation of engines – including the second-generation geared turbofan. The work was pursued under the LuFo Aeronautics Research Program funded by the German Federal Ministry of Economic Affairs and Energy, which has been supporting technology projects geared at reducing engine noise for years.
While the research has taken many different directions since LeiLa was launched in 2012, the line-up of proven partners remained the same as in previous projects of this kind: They included Airbus, MTU Aero Engines, Rolls-Royce and the German Aerospace Center (Deutsches Zentrum für Luft- und Raumfahrt = DLR), plus other research establishments. “The ultimate objective of the joint efforts was to effectively reduce engine noise coming from the fan, combustion chamber and turbine in flight situations such as take-off, cruise and landing, where noise is an issue, using technologies that are feasible,” explains Dr. Stefan Weber, Senior Vice President Technology and Engineering Advanced Programs at MTU. More specifically, the work focused on expanding and enhancing methods of analysis already developed for an improved calculation of sound generation and radiation and efficient attenuation of noise emitted by the fan, turbine and combustor – for example by using novel sound absorbers and optimized turbine blading, and by analysis of sources of sound in enclosed test stands.
MTU Aero Engines focused on its core component – the low-pressure turbine (LPT). MTU project manager Dr. Dominik Broszat, Aeroacoustics Representative: “The sub-project led by us dealt with the expansion of numerical acoustic tools allowing predictions to be made for current and future high-speed low-pressure turbine configurations. In this effort, we cooperated closely with the DLR Institute of Propulsion Technology. Also, we developed and tested low-noise turbine airfoils.” A representative LPT stage was optimally designed from an acoustic and aerodynamic point of view and subjected to experimental testing jointly with Graz University of Technology on a cold flow LPT rig. The quality of the data obtained was very good, and the results are thus ideally suitable for validating the simulation methods developed as part of this and other research projects.
Broszat is satisfied: “We expect to be able to reduce turbine noise by three decibels with the new low-noise airfoils.” The enhanced simulation methods now allow turbine noise to be predicted more accurately and established dependably for the high-speed low-pressure turbine as a special application. Says Weber: “Being able to reliably evaluate and design the constituent parts is a precondition for achieving the ambitious objectives for the module and system in terms of efficiency, weight and costs. At the same time, increasingly stringent requirements regarding noise emissions for emerging engines must be satisfied.”
The new methods afford another benefit: They considerably cut down on the time needed for the acoustic design and evaluation and accelerate the industrial process. The new methods have already been introduced at MTU and are being used for the design of new, low-noise low-pressure turbines for the next generation of engines. The focus is on second-generation geared turbofan engines to power the successors of today’s medium-range aircraft, which are expected to enter into service by the end of the next decade. Another potential application is business jets.
“With the technologies now developed, we strengthen our position as a leading partner for the development of low-noise turbines and once more live up to our reputation of being one of the best turbine makers in the world. This way, we secure high-tech jobs in Germany while at the same time also building the systems integration capability of the German aviation industry in the face of global competition,” summarizes Dr. Jörg Henne, Senior Vice President Engineering and Technology at MTU.
DLR, too, is highly pleased with the results. Prof. Dr. Lars Enghardt, who heads up the DLR Institute of Propulsion Technology’s engine acoustics department, says: “We are happy to have had another opportunity to cooperate closely with our partners from industry under the LeiLa project. Thanks to the ongoing LuFo program, today’s commercial jets are already appreciably quieter than their predecessors used to be. We are working on continuing this trend successfully.“ The DLR further developed numerical methods for predicting noise and conducted comprehensive experiments, for instance for a multi-segmented liner concept.
About MTU Aero Engines
MTU Aero Engines AG is Germany's leading engine manufacturer. The company is a technological leader in low-pressure turbines, high-pressure compressors, turbine center frames as well as manufacturing processes and repair techniques. In the commercial OEM business, the company plays a key role in the development, manufacturing and marketing of high-tech components together with international partners. Some 30 percent of today’s active aircraft in service worldwide have MTU components on board. In the commercial maintenance sector the company ranks among the top 5 service providers for commercial aircraft engines and industrial gas turbines. The activities are combined under the roof of MTU Maintenance. In the military arena, MTU Aero Engines is Germany's industrial lead company for practically all engines operated by the country's military. MTU operates a network of locations around the globe; Munich is home to its corporate headquarters. In fiscal 2015, the company had a workforce of some 9,000 employees and posted consolidated sales of approximately 4.4 billion euros.
Contact
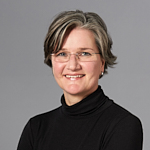
Press Officer Technology