
Press release
Additive manufacturing: MTU Aero Engines steps up its efforts
Munich, May 22, 2018 – The breakthrough came with the borescope boss for the geared turbofan engine powering the A320neo; now MTU Aero Engines is stepping up its efforts in the field of additive manufacturing. At the beginning of this year, a separate department, headed up by Dr. Jürgen Kraus, was set up to push this technology forward. “By pulling all activities – from design to technology development and all the way to production – together in one unit, we want to maintain and build our competitive edge,” comments MTU Chief Operating Officer Lars Wagner.
At MTU’s headquarters in Munich, Dr. Jürgen Kraus, Director, Additive Manufacturing, has assembled a team of around 30 professionals from various technical disciplines: design engineers, structural mechanics engineers, process specialists, and operations scheduling experts. They look into new conceptual designs of applications and constructions from a bionics viewpoint, push the development of the production technology forward, and industrialize the entire process chain. Their work is worth the effort: Experts estimate that by 2030, parts manufactured using additive manufacturing techniques will account for at least 15 percent of the overall engine. “With the development of new machine types and improved online process control, it will be possible to produce an increasing number of components by additive manufacturing in a cost-effective manner,” explains Dr. Jörg Henne, Senior Vice President, Engineering and Technology. The additive manufacturing process used at MTU is selective laser melting, or SLM for short; production of borescope bosses for the PurePower®PW1100G-JM geared turbofan engine powering the A320neo started back in 2013.
Germany’s leading engine manufacturer has ambitious plans: “We are currently pressing on with additive manufacturing, giving its further development top priority in numerous technology projects and technology funding programs,” explains Chief Operating Officer Wagner. The aim is to explore new designs, new components, and new materials. As part of Clean Sky, the largest technology initiative ever launched in Europe, MTU is currently working on a seal carrier manufactured using additive processes. The inner ring with an integral honeycomb structure will be installed in the high-pressure compressor and contribute to improving clearance control, and hence to increasing efficiency. Additional components, such as bearing housings, brackets and struts, will follow. Other aims are to further enhance the process monitoring system and improve the surface finish.
Compelling advantages
MTU embarked on its first foray into additive manufacturing more than ten years ago, for the benefits of the innovative approach are too compelling to ignore: The processes allow the production of complex components that are extremely difficult, if not impossible to manufacture using conventional methods to be produced with only small amounts of material and few tools. The technology opens the door to entirely new designs, appreciably cuts development, production and lead times, and brings down production costs. Says Kraus: “We started off making tools, such as spray nozzles and grinding wheels, as well as parts with a simple geometry for experimental testing.” In the second phase, castings and milled parts were replaced by parts made by additive manufacturing. At around the same time, work on the borescope bosses began to pick up speed. Plans are now to redesign and produce lightweight components in a next step. “MTU is gradually growing the range of parts it produces by additive manufacturing,” according to Wagner.
About MTU Aero Engines
MTU Aero Engines AG is Germany’s leading engine manufacturer. The company is a technological leader in low-pressure turbines, high-pressure compressors, turbine center frames as well as manufacturing processes and repair techniques. In the commercial OEM business, the company plays a key role in the development, manufacturing and marketing of high-tech components together with international partners. Some 30 percent of today’s active aircraft in service worldwide have MTU components on board. In the commercial maintenance sector the company ranks among the top 5 service providers for commercial aircraft engines and industrial gas turbines. The activities are combined under the roof of MTU Maintenance. In the military arena, MTU Aero Engines is Germany’s industrial lead company for practically all engines operated by the country’s military. MTU operates a network of locations around the globe; Munich is home to its corporate headquarters. In fiscal 2017, the company had a workforce of some 10,000 employees and posted consolidated sales of approximately five billion euros.
Contact
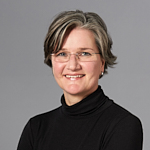
Press Officer Technology